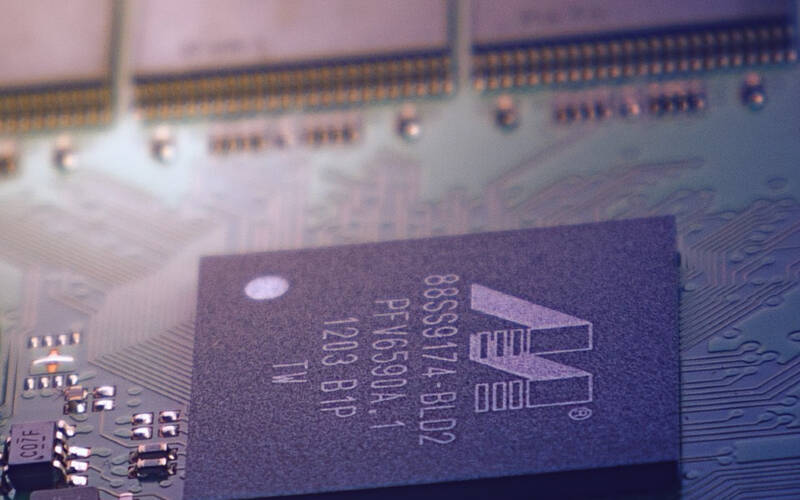
Live system support EQUIPMENT OBSOLESCENCE MONITORING
LSS Equipment Obsolescence Monitoring
the context
When preparing the incident resolution strategy meetings, we provide an aid to decision-making by carrying out the following assignments:
- Entering precise data on a regular basis to a database linked to the changes during production shutdown (stock, consumption)
- Make it usable and correlate it with other databases (including PLM)
- Analysing the effects (criticality, supply times, use cases, origin of the need, date of the need)
LSS Equipment Obsolescence Monitoring
our team
- Since September 2010 at ArianeGroup on the mechanical floor resources and secure infrastructures
- Since February 2017 on all the Thales DMS and military AVS & carriers
The two main detection methods used by the teams are:
- Proactive detection by strategic monitoring (catalogue scanning)
- Reactive detection when taking orders for parts related to purchases
The teams are made up of general engineers proficient in using database tools (Access, etc.) because of the vast range of spare parts families concerned.
The relationship with the customer is very close because the issues concerning the availability of parts/equipment on operational sites are crucial.x.
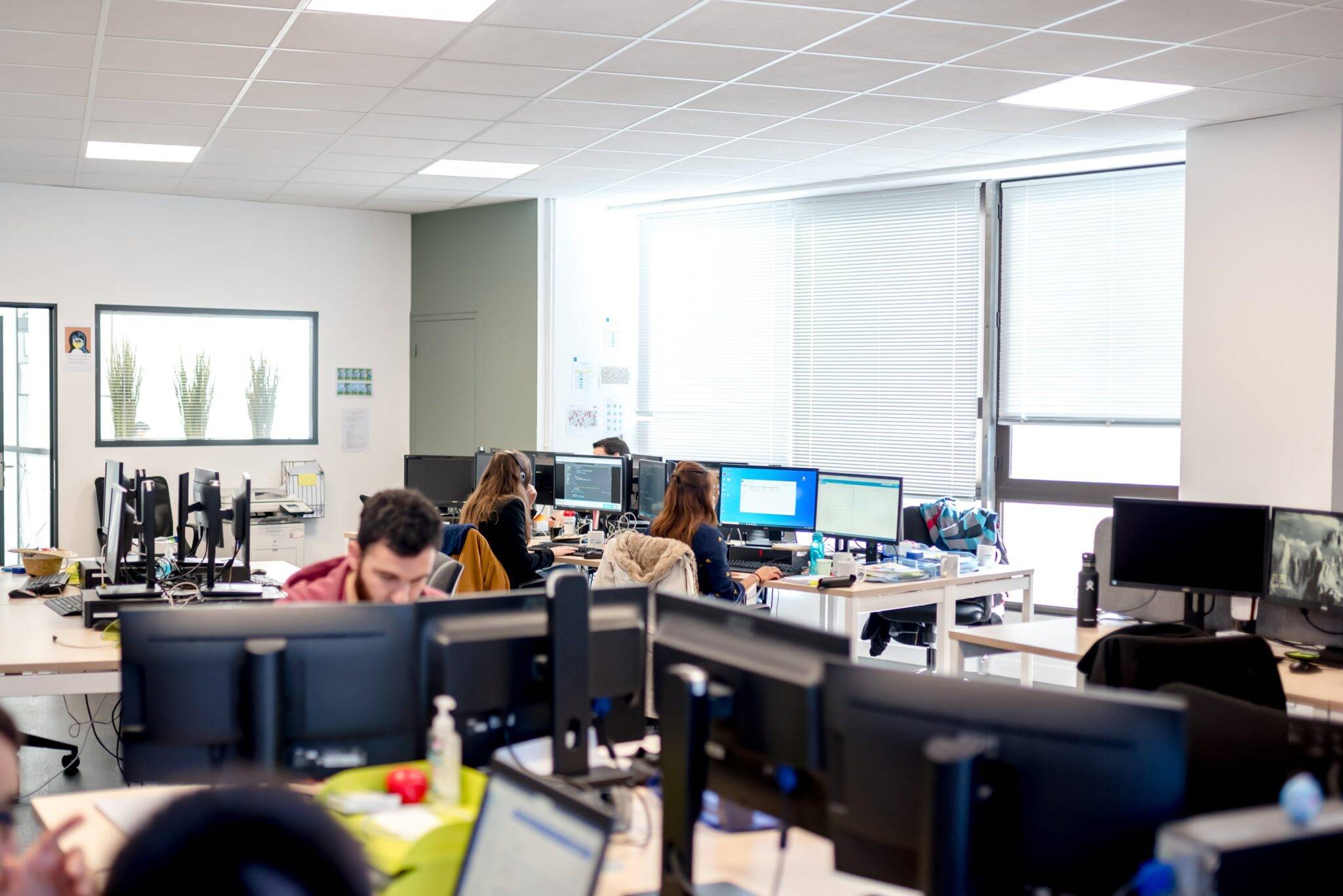
LSS Equipment Obsolescence Monitoring
our support
Apside’s support focuses on 2 main aspects:
Reception and alerting of all detected manufacturing stoppages, Stock and consumption mapping, Updating of collaborative BoD(s), Interface with brokers (component brokers).
Support :
- Search for obsolete technical reference documentation and propose substitutes
- Ensure handover to technical resolution of obsolescence
- Guarantee the overall process (from detection to documentation update)
- Summarize via monitoring indicators
Obsolescence monitoring can be carried out within the following scope:
- All mechanical parts (hardware, parts for lifting and rolling equipment, aeronautical parts)
- All electrical/electronic/electromechanical parts
- Fluids (greases, oils, fuels)
- Others (paints, infra equipment)
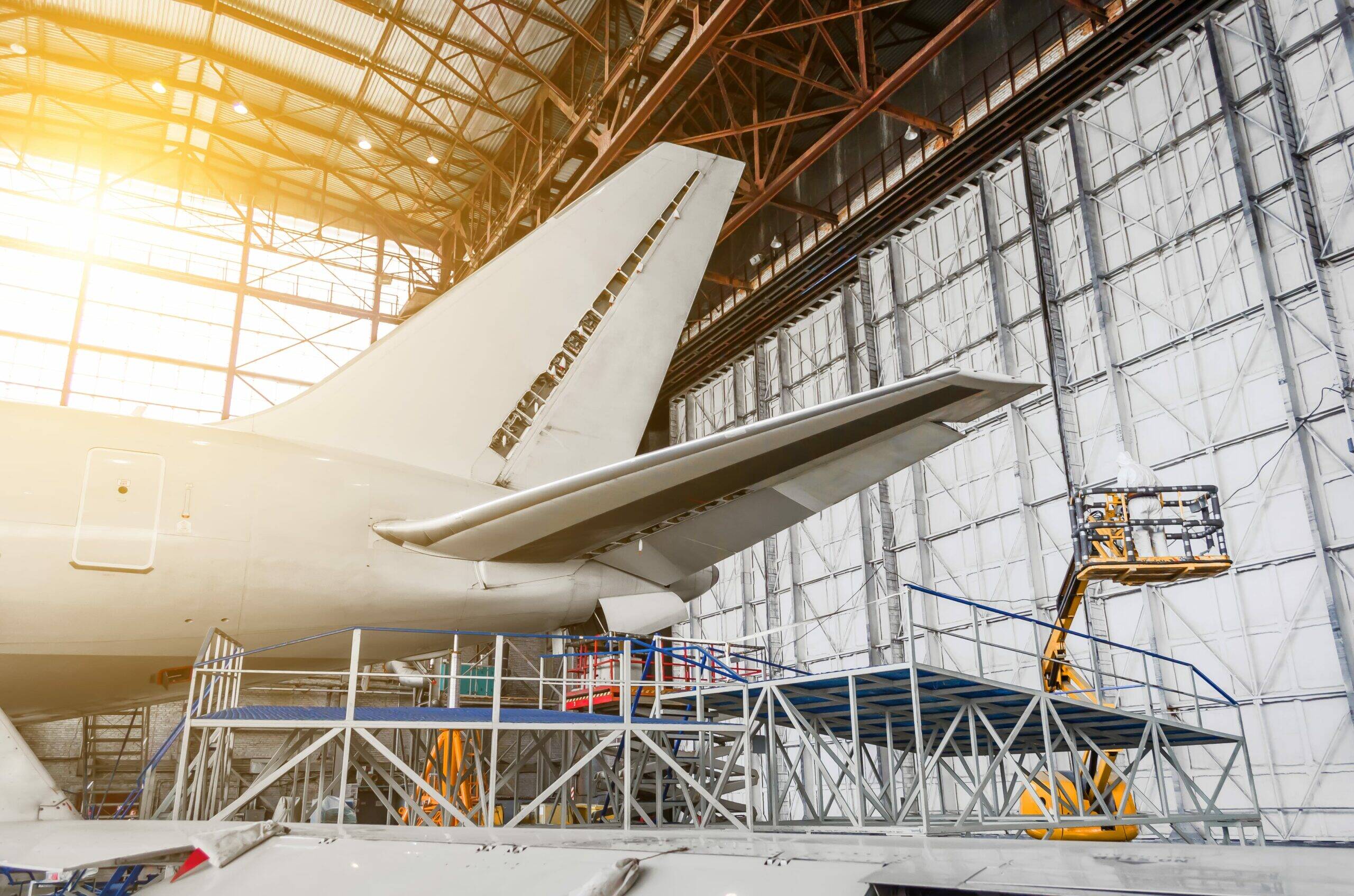
Equipment Obsolescence Monitoring
results and benefits
-
10APSIDIANS
With over
-
+10,000COMPONENT REFERENCES
either
Our support facilitated a significant increase in the capacity to prioritise obsolescence resolutions and to clean up and update the spares database. This created a solid OPEX for design recommendations, selection of spare parts, setting up data flows to build the illustrated catalogue. This also led to the development and implementation of a specific sustainability tool in order to assist in the decision on the status of obsolescence (cross-checking information on nomenclatures, stocks, needs, consumption, etc.)
OUR PROJECTS
Our expertise at the service of your needs
Carry out a project
Do you have an idea for a project, but you don't know where to start? Our team of experts is ready to assist you. Contact us today to discuss your project and find out how we can work together to make it happen.
Contact us